全國服務熱線:【152-4428-9576】
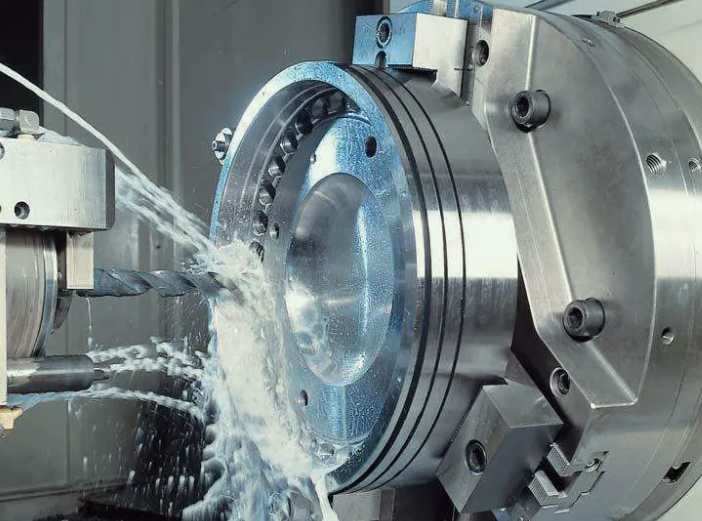
什么是切削液?
切削液(Cutting Fluid)是一種用在金屬加工(切、鉆、銑、車等)過程中,用來冷卻、潤滑工具和加工件的工業液體,用以減少工件的摩擦和磨損。
大部分時候,切削液都被認為是冷卻液(Coolant)或者潤滑液(Lubricant),這不全對,因為除這兩個方面外,冷卻液還有很多其他方面作用
事實上,切削液的使用要追溯到遠古時代—當時,水被用作最初的切削液—類似鑄造過程就是使用水作為冷卻。但是,水在潤滑方面并沒有多大作用,因此經過不斷改進最終形成現在的切削液----它是水和油的混合物(乳化劑使得它們能結合在一起),通過化學物質的添加使得切削液分布更加均勻。
切削液有什么作用?
切削液在金屬加工過程中主要起到以下幾個作用:
1.冷卻(Cooling):通過和發熱的工具(刀具、砂輪等)、切屑和加工件之間的對流和汽化作用把熱量帶走,從而有效地降低切削溫度,減少工件和工具的熱變形,提高加工精度和工具壽命。
2.潤滑作用(Lubricating):通過在工具與工件之間形成潤滑膜,減小切削力、摩擦和功率消耗,降低工具與工件坯料摩擦部位的表面溫度和磨損,改善工件材料的切削加工性能。
3.清洗作用(Cleaning):除去切屑、磨屑以及鐵粉、油污和砂粒等,防止機床和工件、刀具的沾污,使刀具或砂輪的切削刃保持鋒利,不影響切削效果。
4.防銹作用(Anti-rust):在金屬切削過程中,工件要與環境介質及切削液組分分解或氧化變質而產生的油泥等腐蝕性介個質接觸而腐蝕,與切削液接觸的機床部件表面也會因此而腐蝕。此外,在工件加工后或工序之間流轉過程中暫時存放時,也要求切削液有一定的防銹能力,防止環境介質及殘存切削液中的油泥等腐蝕性物質對金屬產生侵蝕。
切削液有哪些?
目前行業上常用的切削液主要有以下幾類:
1.水基切削液(Water-soluble Fluid)
1.1乳化油(Emulsifiable oils)
1.2合成油(Synthetic fluid)
1.3半合成油(Semi-synthetic fluid))
2.切削油(Neat Cutting Oil)
2.1活性(Active Oil)
2.2非活性(Inactive Oil)
3.氣體潤滑劑(Gaseous Lubricants)
空氣、氬氣、氮氣、二氧化碳等
切削液的使用方法有哪些?
按照加油方式可以分為以下幾類:
1.手工加油法(Manual Application)
固體或膏狀潤滑劑可以用毛筆、刷子將潤滑劑涂或滴落到刀具或工件上(主要是攻螺紋、板牙套螺紋時),適用于少量鉆孔或攻牙等。
2.溢流法(Flood Cooling)
這是目前最常見的方法。用低壓泵把切削液打入管道中,經過閥門從噴嘴流出(噴嘴安裝在接近切削區域)。切削液流過切削區后再流到機床的不同部件上,然后匯集到集油盤內,再從集油盤流回到切削液箱中,循環使用。
3.噴霧法(Mist/spray Cooling)
切削液經一個小的噴嘴,使用壓縮空氣將切削液分散成很小的液滴噴入切削區。噴霧法適合于端銑、車削、自動機床加工、數控機床加工等高速切削但是加工區域小的方式;通常油基潤滑劑不建議用噴霧法,因為容易產生油霧污染環境,對人體有害。
4.高壓法(Jet Cooling)
采用高壓大流量向切削區域噴射潤滑液,常用于深孔加工。
5.制冷液體降溫法Chilled fluid cooling
常見用于氣體潤滑劑---將氣體壓縮成液態存于壓力容器中,使用時經過調節閥,由噴嘴直接注射于切削區,靠氣化吸熱來冷卻刀具、工件和切屑。適用于不銹鋼、耐熱鋼、高強度合金鋼等難加工材料的切削加工,可以大大提高刀具耐用度。
切削液怎么樣選擇?
選擇切削液可以從以下幾個維度考慮:
1.根據加工工藝選擇
1.1粗加工:選用冷卻能力強的乳化液或者合成液
1.2精加工:選用潤滑較好的高濃度極壓乳化液或者極壓切削油
1.3孔加工:高粘度乳化液或者極壓切削油
1.4深孔加工:低粘度極壓乳化液或者極壓切削油
2.根據工件材料選擇
2.1鑄鐵/鑄鋁、青銅等脆性材料粗加工時不使用切削液,精加工時可選煤油等低粘度,潤滑性好的切削液
2.2常規鋼材:粗加工時選用乳化液,精加工時選硫化乳化液
2.3耐熱鋼、不銹鋼等難加工材料:極壓切削油
2.4鋁材:煤油
2.5銅材:松香油
3.根據加工工具
3.1工具鋼刀具:冷卻效果好的乳化液
3.2高速鋼刀具:低速加工時,選用潤滑性和一定的流動性好的的乳化液;高速加工時選用水基切削液
3.3硬質合金刀具:常規粗加工時可不加切削液;重切削時加乳化液或者合成液
3.4陶瓷/金剛石刀具:可以不用切削液或者加水基切削液。
全國服務熱線:【15244289576】
全國服務熱線:【15165428330】